河南省科技攻关项目
塑料模具排料系统的智能优化算法研究
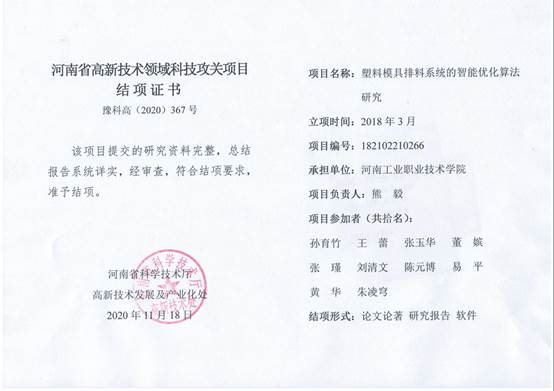
项目主要研究内容
制造业中,通常将多个零件毛坯布局在一个尺寸较大的原料中,以合理的利用边角料。模具设计中的排料,又称拼料,布料等,是将材质相同、几何外形差异较小的同种或同类零件组合在一起进行原材料的采购及加工,同时根据工艺特点设置组合零件排布的规则及参数。传统上采用的人工排料,存在效率低、废料多等问题。首先,在依靠经验进行下料的时候,是按零件形状从板材顺序剪切,多数时候并不能得到整体上的最优结果,造成材料的浪费;二是由于企业不能套料预算,导致大量原材料积压,资金占用严重;三是在下料过程混乱,难以定时定量定额的管理下料过程,生产效率低。随着塑料模具结构复杂程度增加,零件数量越来越多,如果在设计阶段就能准确预测原材料的数量和规格,则能提高排料效率、节省原材料成本。该项目针对上述问题,设计了一种模具零件自动排料系统。
1.开发研究所取得的突破
(1)实现了一键自动排料,解决了人工排料效率低的问题。根据用户选择组件,实现自动计算最小包围盒、调整姿态、分组、创建排料盒子等过程。
(2)提出了一种基于直线边和平直面特征的快速包围盒计算方法。时间复杂降低至O(n),对于一般的三维模型,其实际计算时间仅为0.02~0.07s,大幅提高了包围盒的计算效率,有利于工程应用。
(3)建立了基于集合论的排料系统数学模型,实现了用数学语言描述排料问题。将待排料的所有零件看成是一个集合,每个零件个体看成是一个元素,则实际问题抽象为将一个集合划分为若干个子集的过程。
(4)完成了坐标变换矩阵的求解,正确实现了组件从部件到排料装配的坐标变化。计算了组件由部件中任意位置变换到装配中“正立”位置的变换矩阵。
(5)通过排序和多次分组,实现了不同约束条件下零件的深度分组。按照以X方向尺寸由小到大排序,生成零件的初始序列。分别按X方向的公差约束、Z方向的公差约束及排料盒子长度的上限约束,进行了三次分组,实现了将零件集合划分为若干个子集。
2.对国民经济和社会发展的作用
使用该排料系统,相对于传统方式效率提升50%以上,为企业节约采购成本20%以上。
(1)排料系统减少了模具材料消耗、提高设计人员工作效率。系统提高了材料利用率,减少了锯床、普通铣床的下料工作量,减少能耗、噪声、废水、废渣等污染,有利于环境保护。系统计算速度快,使模具设计人员能够从繁琐的重复劳动中解放出来,专注于创新的工作,推动模具设计水平提高。
(2)基于几何特征识别的包围盒算法具有较好的通用性。包围盒算法计算对象为物体的三维模型,无需对模型离散。算法可广泛用于图像处理、模式识别、碰撞检测、模具分型设计和机械控制等场景。
(3)排料算法经过改进和拓展后可用于其他领域。可以应用到包装领域以及航空、货运、物流等行业的装箱问题中。